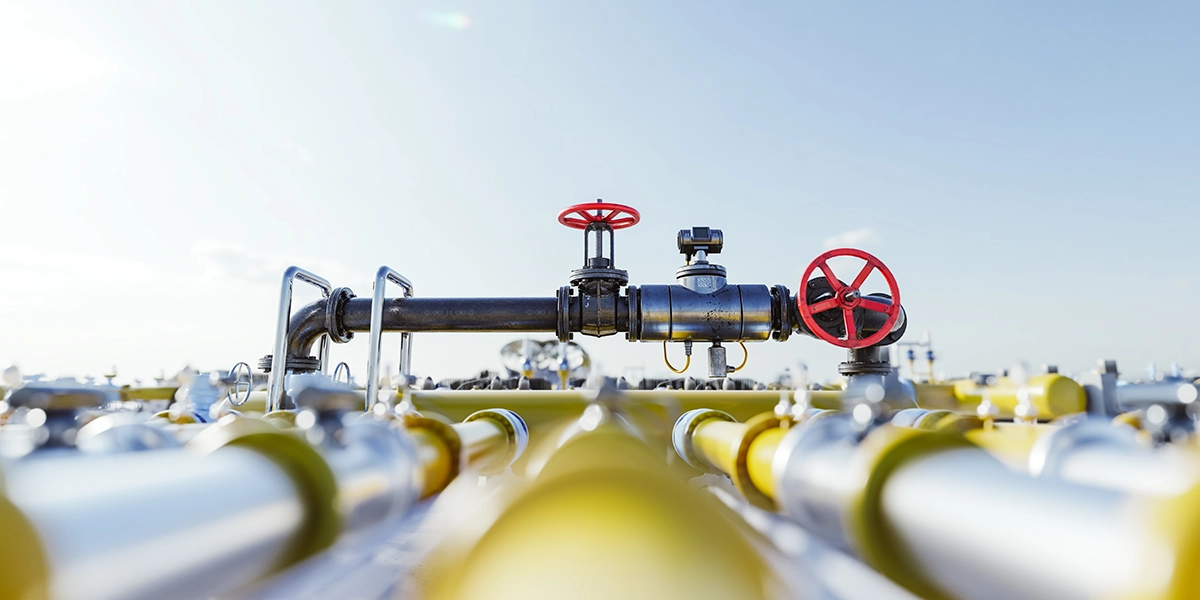
Corrosione nell’industria del Petrolio e del Gas
La corrosione all’interno delle tubature è un problema critico che incide sulla longevità e sulla sicurezza dei sistemi di conduzione. Questo processo, spesso causato da una reazione chimica tra il materiale della tubazione e il suo ambiente, può portare a perdite, rotture e, in definitiva, guasti al sistema. Ecco una ripartizione dettagliata del processo di corrosione all’interno delle tubazioni:
1. Tipi di corrosione
Corrosione uniforme: questa è la forma più comune, in cui la superficie metallica perde uniformemente materiale a causa di reazioni chimiche o elettrochimiche.
Corrosione per vaiolatura: altamente localizzata e porta alla creazione di piccoli fori nel metallo.
Corrosione interstiziale: si verifica in spazi ristretti dove si accumula una soluzione stagnante.
Corrosione galvanica: si verifica quando due metalli diversi sono in contatto in un elettrolita corrosivo.
Corrosione intergranulare: si verifica lungo i bordi dei grani del metallo.
Cracking da corrosione da stress (SCC): risultato dell’influenza combinata dello stress da trazione e di un ambiente corrosivo.
2. Fattori che influenzano la corrosione
Proprietà dei materiali: materiali diversi reagiscono in modo diverso con gli elementi ambientali.
Condizioni ambientali: i livelli di ossigeno, salinità, temperatura e pH possono accelerare la corrosione.
Esposizione chimica: l’esposizione ad acidi o altre sostanze corrosive può aumentare i tassi di corrosione.
Attività microbica: i microrganismi possono indurre la corrosione attraverso processi che generano sottoprodotti corrosivi.
3. Meccanismo di corrosione
Reazione elettrochimica: la maggior parte della corrosione delle tubazioni è elettrochimica e coinvolge un anodo (dove avviene l’ossidazione), un catodo (dove avviene la riduzione) e un elettrolita.
Reazione anodica: all’anodo, gli atomi metallici perdono elettroni e formano ioni metallici, che poi si dissolvono nell’elettrolita circostante.
Reazione catodica: al catodo si verifica una reazione di riduzione che tipicamente coinvolge ossigeno e acqua, consumando elettroni dall’area anodica.
Formazione di prodotti di corrosione: queste reazioni provocano la formazione di prodotti di corrosione, come la ruggine nei tubi di ferro, che possono influire ulteriormente sul flusso e sull’integrità della tubazione.
4. Rilevazione e monitoraggio
Ispezione visiva: ispezioni regolari per individuare segni di corrosione, inclusi scolorimento, vaiolatura e perdite di materiale.
Coupon e Probe: dispositivi posizionati all’interno della tubazione per misurare il tasso di perdita di metallo. Per sapere di più sui nostri Coupon e Probe.
Test ad ultrasuoni: utilizza le onde sonore per rilevare cambiamenti nello spessore della parete della tubazione.
Smart PIG (Pipeline Inspection Gauges): strumenti che viaggiano attraverso la pipeline, raccogliendo dati sulle sue condizioni.
5. Prevenzione e mitigazione
Protezione catodica: Applicazione di una tecnica per controllare la corrosione di una superficie metallica rendendola il catodo di una cella elettrochimica.
Rivestimenti: barriere protettive applicate per prevenire l’esposizione del metallo ad ambienti corrosivi.
Selezione del materiale: l’utilizzo di materiali o leghe resistenti alla corrosione può ridurre drasticamente il verificarsi della corrosione.
Controllo ambientale: modifica dell’ambiente attorno alla pipeline per ridurre gli elementi corrosivi, come il controllo del pH e dei livelli di ossigeno.
Iniezione chimica e campionamento: dall’analisi dei dati il cliente può ottimizzare l’uso di inibitori e programmi di ispezione e manutenzione per prolungare la durata dell’impianto e delle risorse. Per sapere di più sul Chemical Injection and Sampling System clicca qui.
Comprendere e mitigare la corrosione nelle condutture è fondamentale per mantenere l’integrità e l’efficienza di queste infrastrutture vitali. Una manutenzione regolare, combinata con tecnologie di monitoraggio avanzate, può aiutare a prevenire guasti catastrofici e prolungare la durata dei sistemi di condutture.