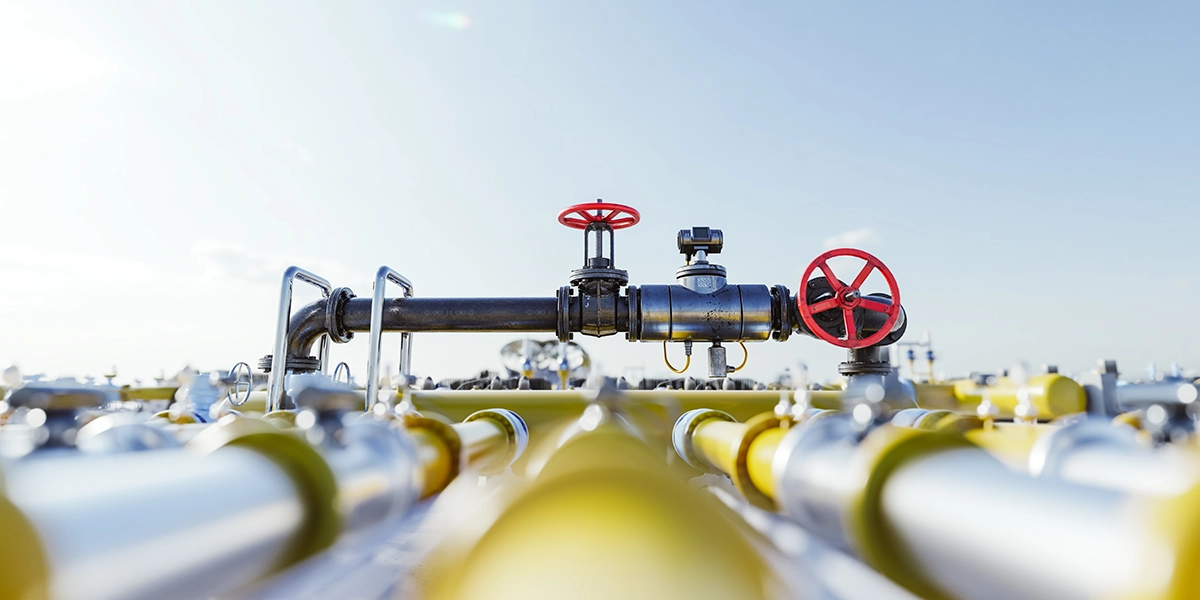
Corrosion In Oil & Gas Industry
Corrosion inside pipelines is a critical issue affecting the longevity and safety of pipeline systems. This process, often caused by a chemical reaction between the pipeline material and its environment, can lead to leaks, ruptures, and ultimately, system failures. Here’s a detailed breakdown of the corrosion process inside pipelines:
1. Types of Corrosion
Uniform Corrosion: This is the most common form, where metal surface uniformly loses material due to chemical or electrochemical reactions.
Pitting Corrosion: Highly localized and leads to the creation of small holes in the metal.
Crevice Corrosion: Occurs in confined spaces where a stagnant solution gathers.
Galvanic Corrosion: Happens when two different metals are in contact in a corrosive electrolyte.
Intergranular Corrosion: Occurs along the grain boundaries of the metal.
Stress Corrosion Cracking (SCC): A result of the combined influence of tensile stress and a corrosive environment.
2. Factors Influencing Corrosion
Material Properties: Different materials react differently with environmental elements.
Environmental Conditions: Oxygen, salinity, temperature, and pH levels can accelerate corrosion.
Chemical Exposure: Exposure to acids, bases, or other corrosive substances can enhance corrosion rates.
Microbial Activity: Microorganisms can induce corrosion through processes that generate corrosive by-products.
3. Mechanism of Corrosion
Electrochemical Reaction: Most pipeline corrosion is electrochemical, involving an anode (where oxidation occurs), a cathode (where reduction occurs), and an electrolyte.
Anodic Reaction: At the anode, metal atoms lose electrons and form metal ions, which then dissolve into the surrounding electrolyte.
Cathodic Reaction: At the cathode, a reduction reaction typically involving oxygen and water occurs, consuming electrons from the anodic area.
Formation of Corrosion Products: These reactions result in the formation of corrosion products, such as rust in iron pipes, which can further impact the flow and integrity of the pipeline.
4. Detection and Monitoring
Visual Inspection: Regular inspections for signs of corrosion, including discoloration, pitting, and leakage.
Corrosion Coupons & Probes: Devices placed inside the pipeline to measure the rate of metal loss. Know more about Coupons & Probes .
Ultrasonic Testing: Uses sound waves to detect changes in the thickness of the pipeline wall.
Smart PIGs (Pipeline Inspection Gauges): Tools that travel through the pipeline, gathering data on its condition.
5. Prevention and Mitigation
Cathodic Protection: Application of a technique to control the corrosion of a metal surface by making it the cathode of an electrochemical cell.
Coatings and Lin ings: Protective barriers applied to prevent exposure of the metal to corrosive environments.
Material Selection: Using corrosion-resistant materials or alloys can drastically reduce the occurrence of corrosion.
Environmental Control: Modifying the environment around the pipeline to reduce corrosive elements, such as controlling the pH and oxygen levels.
Chemical injection & Sampling: From data analysis the Client can optimise the use of inhibitors, inspection and maintenance programs to extend the plant and assets lifetime. The Corrosion Monitoring and analysing must continue in order to assure any changes can be detected and corrected on time. To know more about Chemical injection and sampling systems click here.
Understanding and mitigating corrosion in pipelines is crucial to maintaining the integrity and efficiency of these vital infrastructures. Regular maintenance, combined with advanced monitoring technologies, can help prevent catastrophic failures and extend the lifespan of pipeline systems.